Climate technologies require enormous amounts of metal. I’m Ian Morse, and this is Green Rocks, a newsletter that doesn’t want dirty mining to ruin clean energy.
This edition was written with Asia Undercovered, a three-year-old newsletter that highlights issues in Asia that pass by most media without notice. It’s written by Nithin Coca, who reports stories about interconnections across borders.
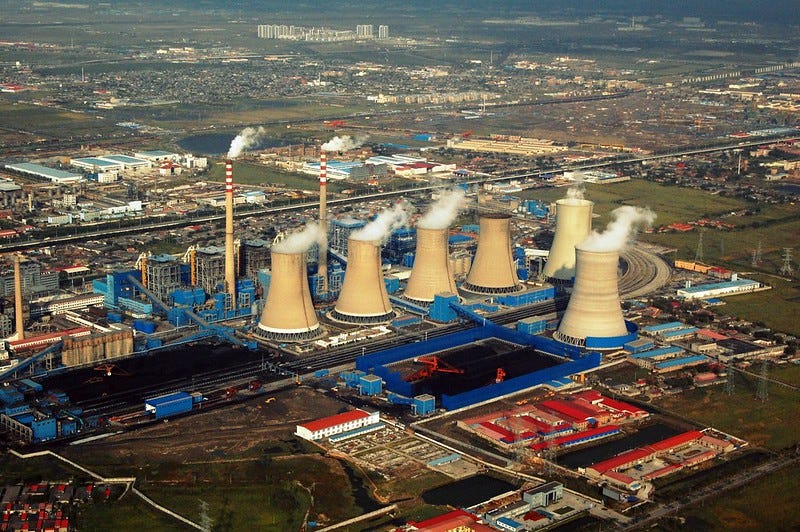
On Sunday, world leaders gather for the most important international climate meeting since Paris in 2015.
For as long as the meeting has taken place, activists say, it has been unequal. It has often taken place in European countries, like this one in the UK. That barrier that has hardened with unequal access to coronavirus vaccines and strict travel hurdles. A third of Pacific Island states, for example, cannot attend due to reduced budgets and quarantine requirement.
It’s hardly a coincidence that the countries which will struggle to attend are also feeling the worst of climate impacts. Had the balance always been tipped in their favor, temperatures may never risen early where they are today. Solutions like micro-grids, two-wheeled electric transportation, and local agriculture might be much more popular.
A western bias has not encouraged attendance from China’s President Xi Jinping, who leads the world’s biggest emitter. He may not attend, which could sink chances of cooperation with the second largest emitter, the US.
Asia, like much of the world, supports contradicting policies regarding climate. Last month, China ordered its coal mines to ramp up production and bought heaps more coal from its primary coal partner, Indonesia. Traversing the same seas, however, were materials that companies believe will save the world from coal.
Those cargo ships carry nickel from Indonesia. Nickel is used in batteries for electric vehicles and stationary storage, as well as steel, which is a much larger proportion of output. Batteries, however, carry the most weight in marketing schemes and both Indonesian and Chinese government development programs. More mines and more smelters, it’s often said, will bring economic development and also satisfy scientists’ calls for renewable energy infrastructure.
Nickel is just one in a grab bag of metals that have been slated to deliver energy into a modernistic, emissions-free future. Lithium, cobalt and rare earth elements are often uttered in the same breath, but graphite, iron, and tin often play just as big a role in the transition. Copper and aluminum, especially, are predicted to receive demand jolts that will surpass historic production.
And conversations on these metals rarely forget to mention Asia, and in particular China. China produces an overwhelming majority of important minerals and metal products for solar panels, wind turbines, and EV batteries. The production has come with allegations of health-threatening pollution and labor abuses. For example, a third of the world’s polysilicon for solar panels originate in Xinjiang, where Uighur people are sent to concentration camps and forcibly sterilized, among other tactics in China’s cultural war against them.
If China doesn’t mine these materials, often it is Chinese companies that refine and combine it into these products. With a global push to spread climate technologies, Chinese companies are poised to benefit in a colossal way.
As a result, national security hawks of the US and Europe who hadn’t previously paid attention to clean energy technology, now worry their countries will lose out in this global project to stop warming the planet. Governments in the US and Europe are designing new policies that cite energy independence to invest in domestic mining and manufacturing. The US, in particular, has in the past few years prioritized aggressive trade policy over expanding cheap climate technologies. That has led some groups, like the Center for Strategic and International Studies, to recommend that for the sake of climate, the US could create a more amicable relationship with China.
Like with much coverage of China, anglophone media have echoed these politicians. Outlets struggle to find productive language to describe the country’s production of materials. China’s presence in the industry has been described as a “grip”, “stranglehold”, “dominance” or “control”.
Yet this anti-China resource nationalism is not borne out by Chinese actions. Regulatory changes reveal the country isn’t keen to retain that “tight grip,” nor can it with dwindling reserves. As a result, some Chinese companies in the past 15 years have begun to search abroad for mineral deposits it can import. In these projects, Chinese companies can be the target of social and environmental conflicts, but they aren’t as easily distinguished from their political rivals.
In Guinea, for example, Chinese companies work in tandem with European conglomerates. While media narratives focus on rivalries between the three largest GHG emitters, international banks boost mining projects for both, which send most of their products to China. Meanwhile, Guinean communities don’t feel they have a seat at the table. To cite another example, US projects to produce rare earth elements for use in electric motors for renewable energy, pit investors against hegemonic Chinese projects. The Chinese government, however, is bolstering environmental standards, which have pushed mining investors to look abroad for projects.
So, in the end, China has joined the US and Europe in outsourcing natural resource projects to areas where pollution doesn’t receive as much pushback.
The rivalries over mining and materials end up distracting policymakers from actions that not only reduce the need for mining, but may also be far faster. Mines typically take decades to build, because only large-scale projects, which require mountains of capital, can find a place in the market for ever cheaper electric vehicles that are luxuries to the world outside the US and Europe. Initiatives to build public transportation, electrify heavy duty transport, communal car-sharing, and reductions in energy consumptions have the potential to be faster and bigger bangs for bucks.
Building up domestic manufacturing in the US and Europe may have a crucial advantage: recycling. When climate plans encourage millions of people to swap gas-burning cars for electric, millions of batteries will eventually reach the end of their working lives. But it’s not clear how all will be recycled, a step that would shrink pressures to build more mines. Manufacturing close to the source of millions of used batteries will likely raise the chances that the majority of each battery will actually be recycled, rather than burned and tossed.
China’s government was the first to begin to make electric vehicle companies responsible for recycling the batteries they produced. In the wake of that regulation in 2018, major EV company BYD created a battery that was designed to be easily recycled. Scientists believe it’s a promising step toward products that fit into a circular economy — one where materials don’t end their lives with the consumer, but return for reuse.